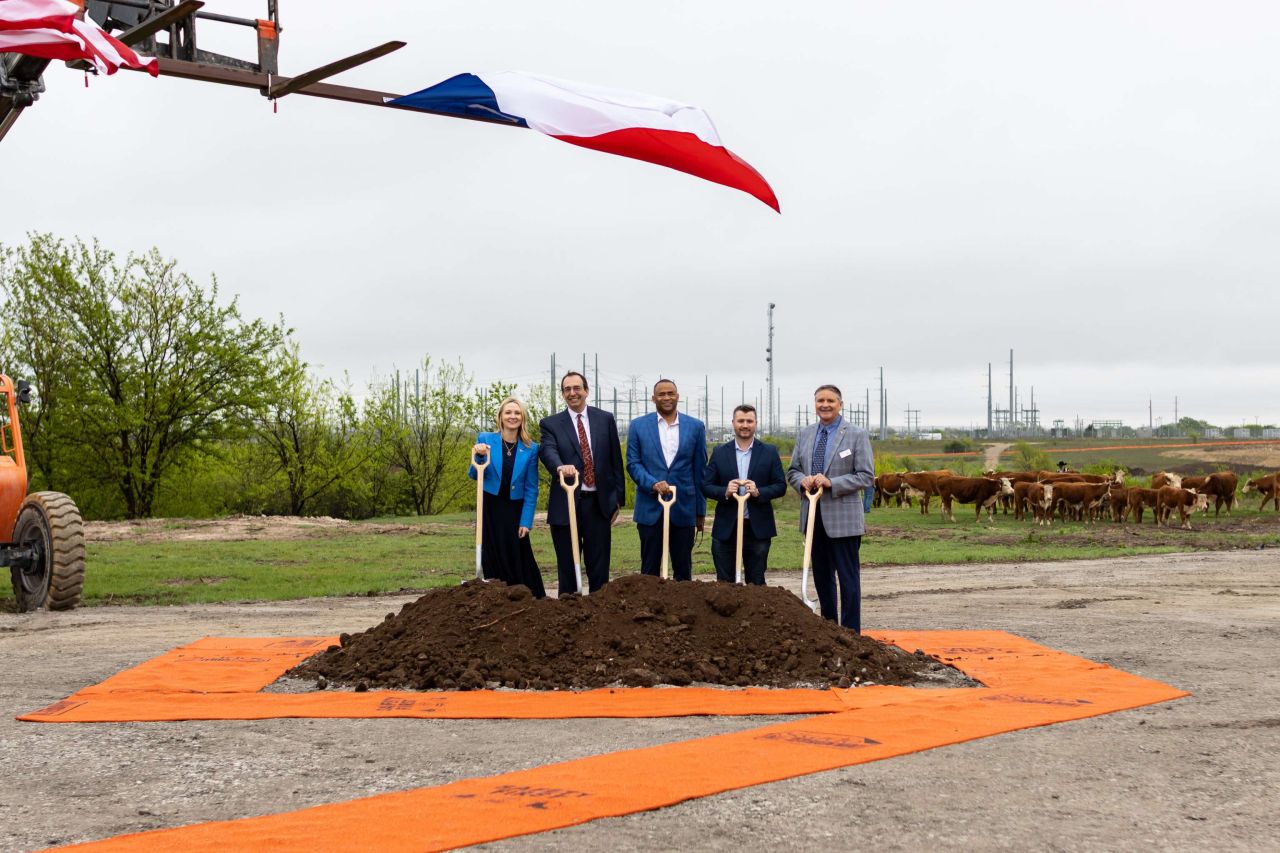
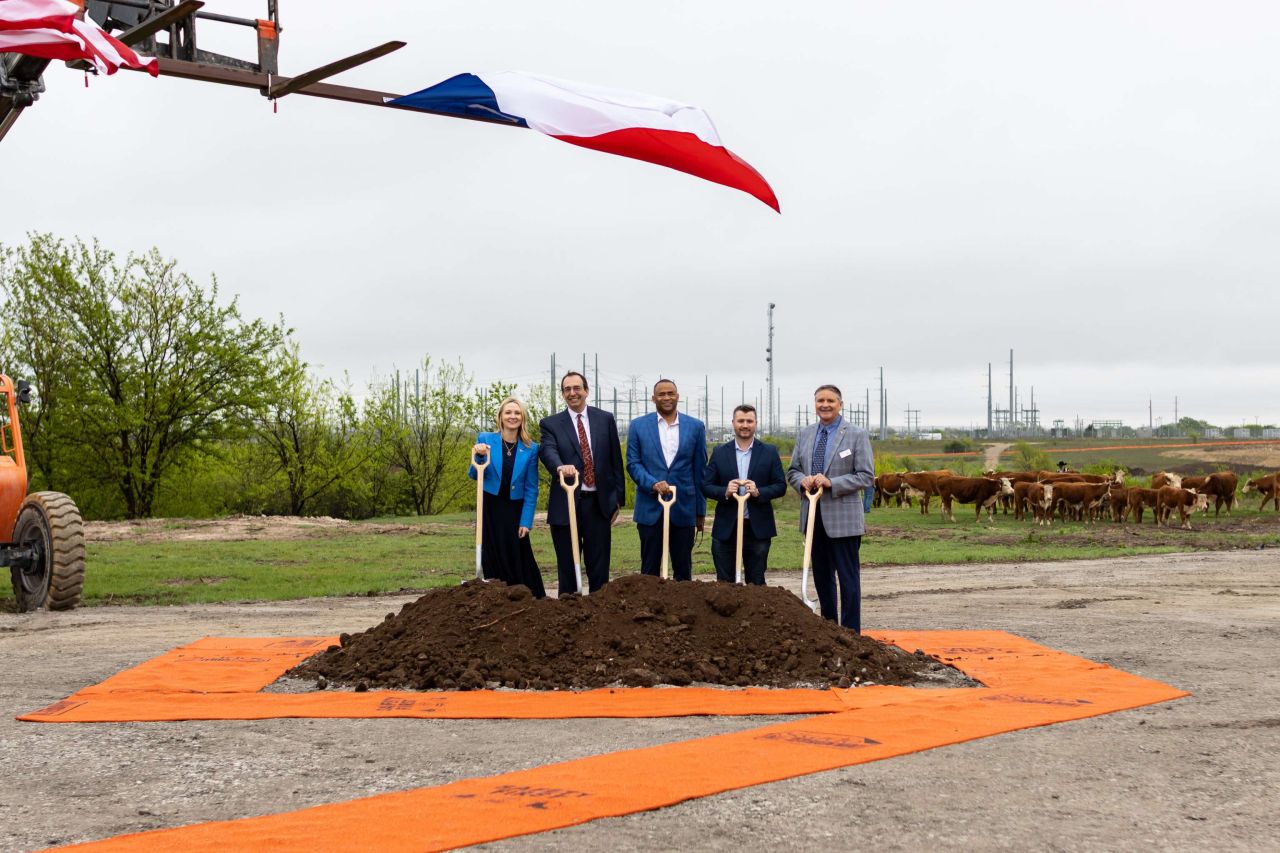
17 February 2022
By: Luke Unverzagt
With data center space an essential component to everyday business and personal functions, the demand for data center construction has continued to skyrocket. The ongoing global supply chain crisis has presented significant challenges to meeting this demand. A lack of raw material inventory at manufacturing facilities, coupled with the continuing labor shortage, has resulted in supply chain delays hitting the construction industry particularly hard.
Like in every market sector, material delays have been unavoidable in data center build-outs. But unlike other sectors, the need for fast-paced schedules is extremely critical. In addition, data centers face unique supply chain issues, because they mostly require major equipment, as opposed to paint or drywall that is needed for traditional interior build-outs. The industry is now seeing severe delays in the manufacturing and delivery of nearly every piece of critical equipment and materials.
The result has been a significant increase in the lead times of deliveries to jobsites. The high quantity of orders being placed for critical equipment is putting an even greater strain on the construction industry to meet the aggressive schedules of data center clients.
What’s the solution?
Because data center space is such a critical component of our daily lives, slowing down the construction process is not a viable option. The planning of all data center construction projects needs to start as early as possible. Early planning allows material and equipment procurement to be predicted and worked into a project’s construction schedule, decreasing the likelihood of delays once the project begins.
Data center construction is especially unique due to the “speed to market” ideology. What this means is in a specific market, whether it’s in Chicago, Virginia or any other data center hot spot, there are many firms working toward the same goal. Getting a data center client’s facility operational quickly to accommodate a lease will help them secure a deal over a competitor and realize profit sooner. Building a data center on schedule takes careful planning, both short and long term.
Clune’s best practice has been to engage with our data center clients and thoroughly understand their vision for current and future projects. This allows us to evaluate material and equipment quantities required to fulfill these build-outs. Once we are able to establish quantities, our teams can provide current lead times and associated pricing. We can compare this information with the master schedule and advise our clients on when to place an order, enabling them to stay on schedule.
If the client’s vision consists mainly of future projects, Clune’s project team discusses if they should order the equipment for these projects immediately to avoid delivery delays. We help them examine all factors of their project, and the pros and cons of different solutions to supply chain issues. Factors Clune has its data center clients consider include:
Working with clients to make decisions with a big picture lens can be one of the most useful steps in making their data centers operational as quickly as currently possible.
Human Error
Unfortunately delays in receiving raw materials is not the only contributing factor to supply chain issues. Human error, especially when fabricating the complex equipment that data centers demand, is common. To decrease the likelihood of human error, Clune has made a practice of visiting factories during the manufacturing process to check on progress. This ensures the equipment is being built per the approved shop drawings and meets the design specifications. If our teams find errors, we work with the manufacturers to develop a plan to take corrective action as soon as possible. The main goal of a correction plan is to prevent shipping delays. While this isn’t always possible, especially when additional long lead materials are needed, it still prevents the scheduling impact that would occur if the incorrect equipment arrived on-site.
Our teams also aim to catch pre-manufacturing human errors. Before reaching the end user, the product has to go through each manufacturer’s process of approving shop drawings. If there is even a typo in one of these steps, the product’s quality can be affected or the delivery date can be miscommunicated. This is why our teams have determined our best practice is to take ownership of monitoring the equipment through the entire supply chain.
Ensuring Your Project is Completed on Schedule
Supply chain issues and labor shortages have made it challenging to complete schedules on time. The only place our teams can control adjustments is in the field. We can attempt to stay on schedule after a major delivery delay by evaluating an increase in trade power on-site. Clune evaluates this based on the following criteria:
In addition to these items we evaluate the cost versus benefit against productivity and safety. Because we have found that tradespeople typically start to lose productivity after 10 hours, we avoid working 12-hour days if at all possible. Additionally, data shows that longer hours result in an increased risk of safety incidents. Based this criteria we determine what work schedule is best for each project. This can be six 10 hour days, five 10 hour days and one 8 hour day, or two different crews working two separate 8 hour shifts per day.
While supply chain issues have forced many construction projects to adjust their timelines, the constant demand for more corporate data center space doesn’t allow for this kind of flexibility. Clune knows it is essential to bring data centers to market quickly. Our top tier practices ensure there is no down time once a facility is operational. We are constantly evaluating best practices so we can bring innovative solutions to the table when our clients need them most – even during a supply chain crisis.