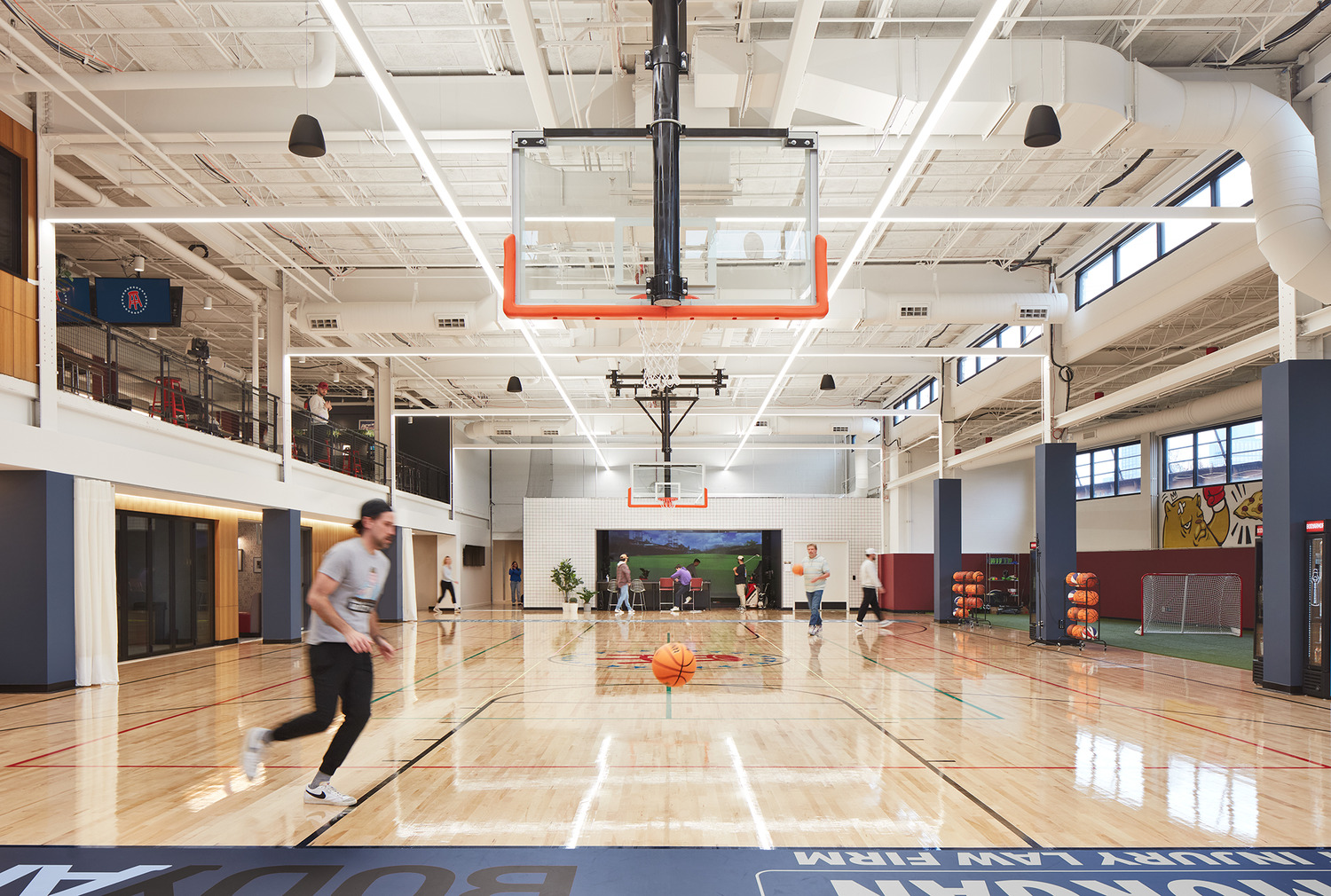
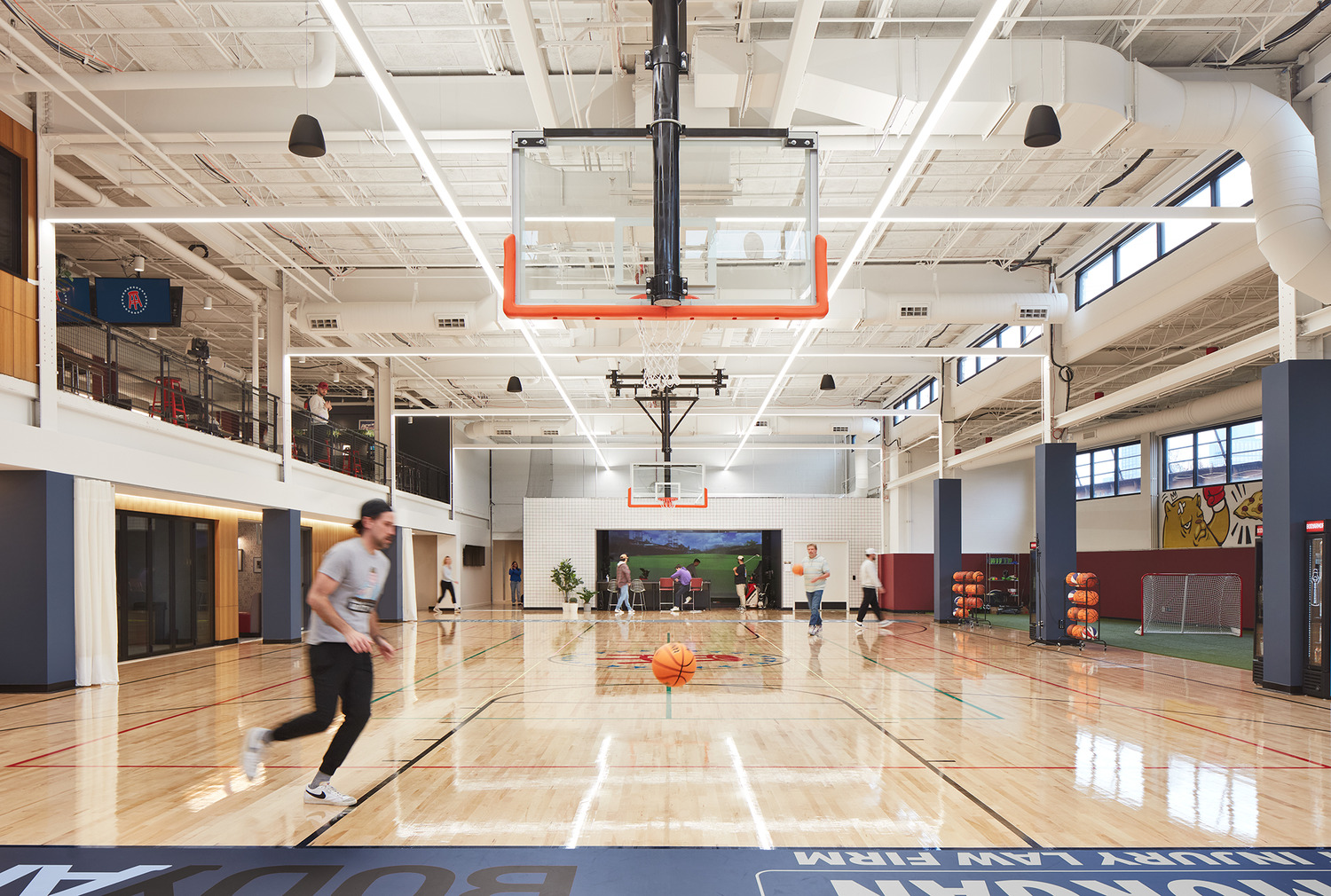
22 July 2021
By: Colin O’Connell, Vice President, Project Executive
Located on at 44 Montgomery St., Boies Schiller Flexner’s (BSF) new San Francisco office represents a new trend in legal work places in the Bay area. It focuses on how attorneys and clients work and collaborate. The space was designed by Schiller Projects with local representation by Cole Design. Clune Construction served as the project’s general contractor.
The construction team members working on BSF’s San Francisco office executed a build-out which included many one-of-a-kind custom features and advanced design elements on a condensed 26-week schedule. The speed and complexity of the project meant that the entire construction team had to perform at their highest level.
Advanced Design Elements
The project consists of several advanced design elements and challenges, including the centerpiece of the project – a custom lit ceiling element at the reception/conference areas that included LumenWerx Lighting + Ceiling Stretched System. It was the first of its kind installed in San Francisco.
Also included in the space are meeting rooms with curved glass walls, a folding glass front system, a custom-build reception desk, 13 enclosed partner offices and 26 open associates’ spaces. In addition, the office houses a variety of conference rooms from single person call rooms to multi-purpose lounges, formal conference spaces and a convertible presentation center with beautiful views of the San Francisco skyline.
At the end of the reception area is a conference room which can be converted from a closed conference center to an open presentation and event space. Located at the focal point of all circulation routes throughout the facility, this space fosters community and collaboration within the workspace.
Schiller Projects and Cole Design designed the space taking cues from technology companies and the constant change of Silicone Valley. The new office design, which expanded BSF’s space by a full floor, solidifies flexibility and integration in an environment that is distinctly future-looking and grounded in a connection to the city itself.
Overcoming Logistical Challenges
Due to the BSF project’s presence in the heart of the Financial District, workers had to overcome several logistical challenges that required extensive coordination by the project team. This included strict working hours, specific hauling routes and working in an area with limited access.
In addition, BSF’s space was located on the 41st floor of a 42-story building that does not have a traditional loading dock. To transport the project’s glass systems, materials had to be brought through the building, then transferred to the basement level finally be to transported up the main freight elevator to the jobsite.
Custom Light Box Installation
Installation of the custom lit ceiling element in the reception area required intense coordination both with the project team and the City of San Francisco. In order to properly install the light box, the project’s electrician and drywall installer had to lay out material on the ground below precisely how they would be installed in the ceiling. Cut outs for the light were made in the drywall, and fit in the fiber glass quarter rounds.
Being the first time a lighting element of this kind was installed in San Francisco, the project team had to get permission from the city to install the plastic fabric that the light transfers through. Permission was also required to service the lighting in the future.
Unique Materials on a Condensed Schedule
When the design and construction team took on the BSF San Francisco project, there were many concerns at the beginning. This included navigating lead times due to the highly unique products that were specified on a condensed schedule.
The high-end finish materials used throughout the office space were sourced from various places around the world. The fabric stretching over the light box element was ordered from France by a supplier in New York and all of the modernist glass was brought in from Los Angeles. The curved glass came from a specialty shop in Mexico, and the glazing extrusions were all fabricated in Italy.
A blue epoxy finish was applied to the floor in the reception area. In order to obtain the exact sheen and color of the flooring, multiple applications were required. Each application required prepping (sanding) of the area, while taking steps to avoid damage to the surrounding finishes.
When the 26-week construction schedule was shortened to 20-weeks, the construction team rose to the challenge and tackled an unprecedented design for the region, delivering the project on-time and on budget for the clients. This included integrating long lead times for the arrival of the custom millwork finishes into the schedule, coordination for safe transport into the space, as well as long dry and cure times, once installed.
Extensive Collaboration
Both design firms played a strong role in the project’s design and execution. Schiller Projects made the selection for the space’s high-end finishes, while Cole Design played a very hands on role on the jobsite, and was extremely selective in choosing the appropriate wood finishes for the space. Cole Designs was also on-site regularly to ensure the design elements were installed according to the design standards. There was extreme and constant coordination between Schiller Projects, Cole Design and Clune Construction to ensure the success of the project.
The construction team rose to the challenge of the innovative design, opening the possibility of unique and high-end design elements for future interior build-outs in the city of San Francisco.
About the Author:
Colin O’Connell is a Vice President, Project Executive in Clune Construction’s San Francisco office. He has nearly 20 years years of experience in the construction industry, and has overseen many high-end tenant improvement projects throughout the San Francisco. Colin has a Bachelor of Science degree in Building Construction Management from Purdue University.