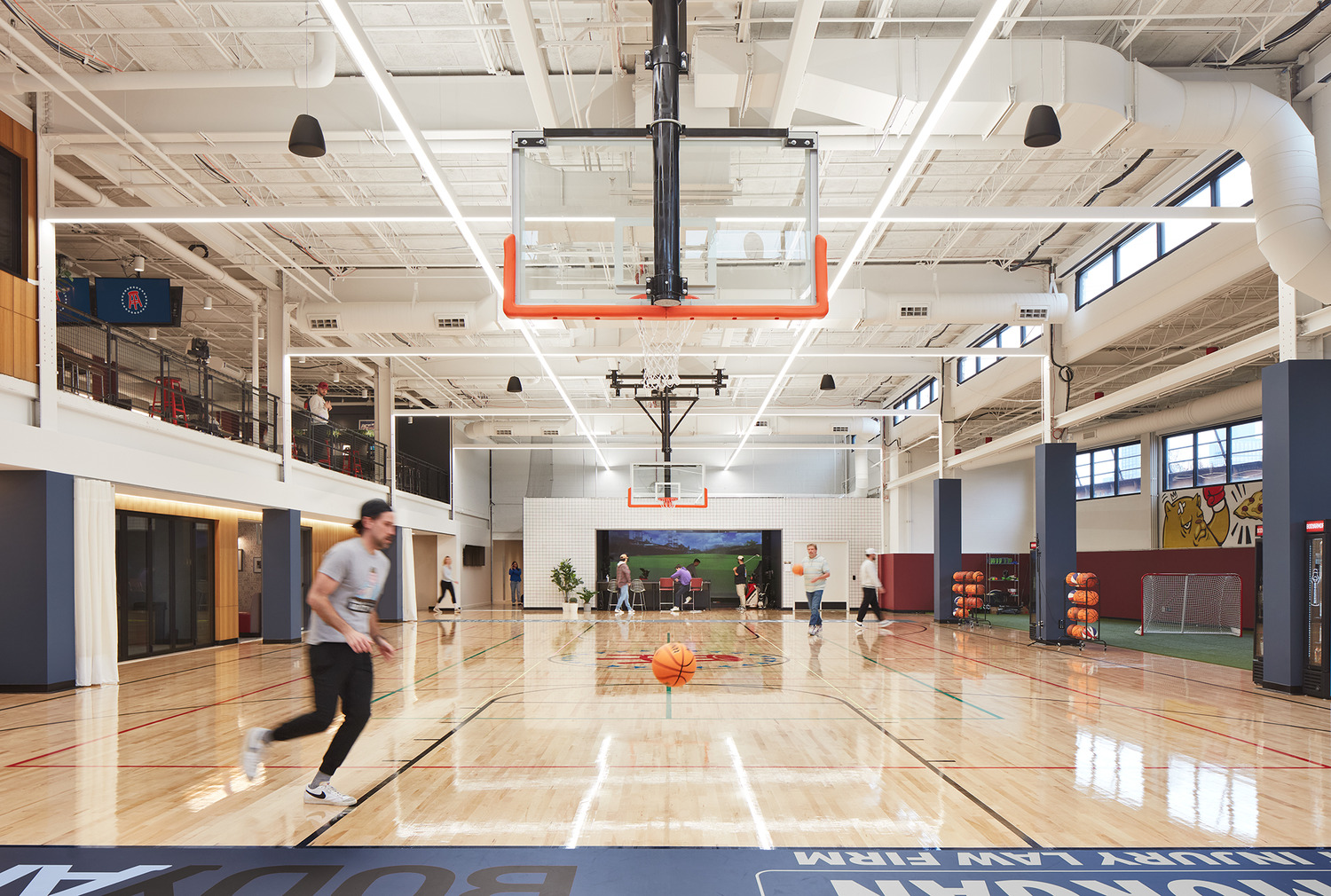
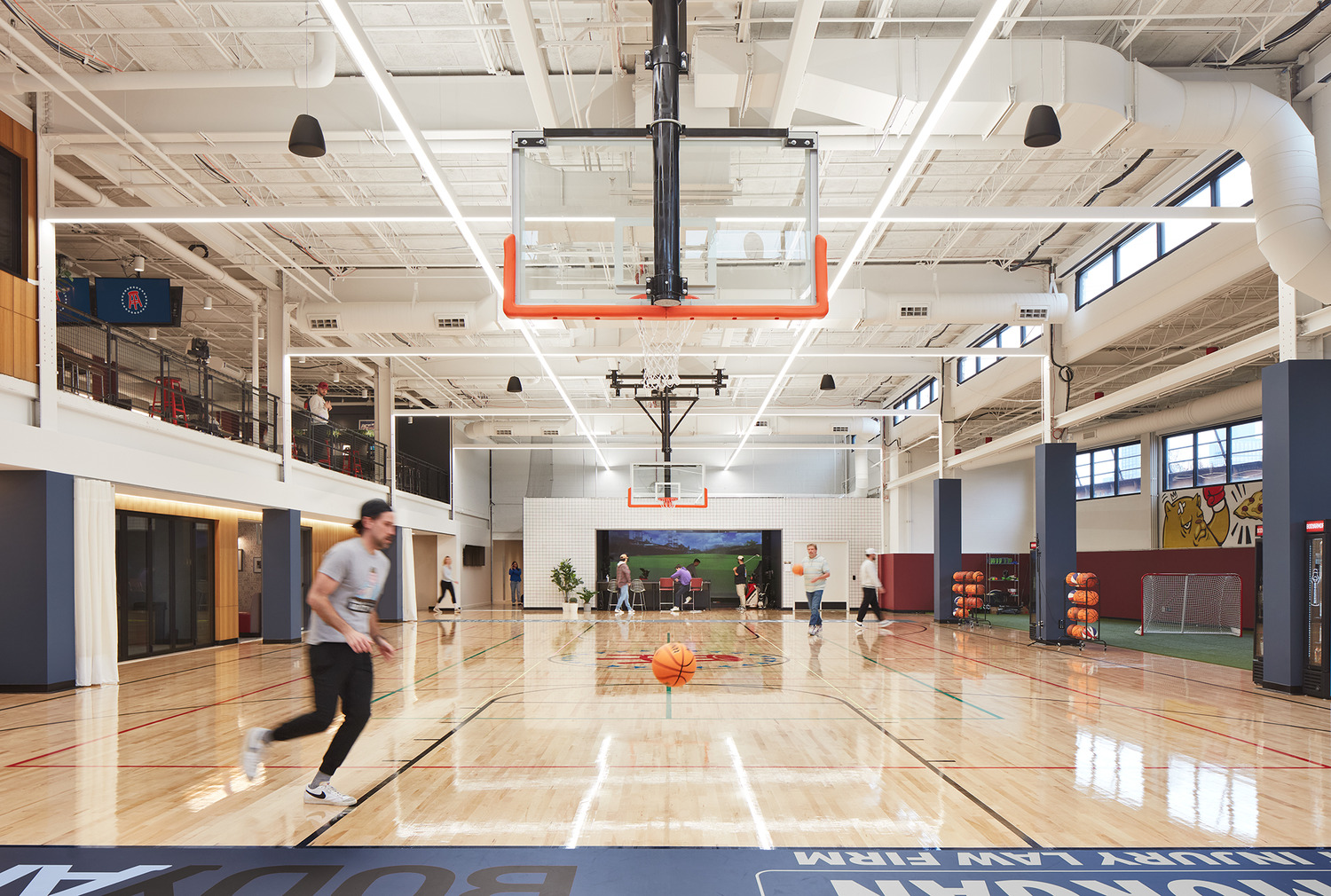
28 February 2022
By: Dan MacNamara
Power over Ethernet (or PoE) lighting, is a trend we expect to see a lot more of this year. PoE lighting allows facility managers to have individual control over every light in their space in order to adjust them for employee comfort, maximize energy efficiency and optimize lighting schedules. Among the first of its kind installed in Chicago, the PoE lighting in Dentsu International’s six-floor office gave our team the opportunity to get in on the ground floor of learning about this next generation technology that will enhance the end-user experience.
Like all new technologies, Dentsu’s PoE lighting installation came with a learning curve during the project and a list of lessons learned at the end. The team spent a lot of time working through the challenges of this new system. They were in regular communication with vendors to come up with solutions to issues that arose, and the potential cost implications. By installing this new lighting system in such a big space, the entire team (including the designers, subcontractors, and vendors) was able to walk away with better knowledge of best practices for future installations. Below are the top 3 lessons Clune learned on our first PoE lighting project.
1. Research Code Compliance
From the very beginning, Clune’s team needed to work with the design team to coordinate the lighting to be in compliance the City of Chicago’s PoE lighting code. The current Chicago PoE code is more vague than other codes due to it being new to the market. The team was required to run the 18/4 cable separately in J hooks in rather than running it in a cable tray, which was the original design. Going forward, knowing this is required we can be more aware of potential issues that could arise with the design. Consulting an inspector when the bid documents are released will help trade partners provide more accurate bids at the beginning of the project. It will provide a more accurate idea of what is required to pass inspection at the end of the project.
We also learned that when it comes to code compliance, mock-ups are your friend. Mock-ups for PoE emergency lighting simplify the process of confirming compliance – it was much easier to show an inspector our plans than to tell them. We learned that with PoE, the emergency lighting needs to be completely hardwired, and can’t work on the same system as the rest of the lighting. This protects the space if the IDF room goes down, the emergency lighting will still go on
2. Detect and Prevent Issues with Product Compatibility
One of the largest coordination elements at Dentsu involved sourcing the lighting from manufacturers. Many manufacturers advertised that their products were compatible with PoE lighting, but when the materials arrived, subcontractors needed additional parts to successfully complete the installation. Many fixtures that arrived on-site didn’t initially work with the PoE system because they didn’t have the correct amount of drivers or gateways figured. Many discrepancies were found with manufacturer lighting fixture cut sheets versus the actual fixtures coming on-site. It was a team effort to identify these discrepancies and come up with quick solutions to keep on-schedule.
To mitigate this, Clune recommends getting the team members onboard as early as possible. Once the team is assembled, do a detailed page turn to review the fixtures and establish a lighting schedule. This can help minimize discrepancies and help the electrician identify potential issues before orders are placed or material arrives in the field. It is also helpful to order extra gateways. Gateways are the component that communicates between the lighting functionalities and the system, providing the data needed to control and monitor the fixture. Not having enough of this material can hold the installation process back, and even if there are spare parts at the end of the project, they can be useful attic stock.
3. Testing Takes Time
It’s critical to allow enough time in the schedule for commissioning the system and training the end users. We performed a lot of troubleshooting at the end of the project, because a light wouldn’t turn on or would flicker. When issues like this come up, the first thing to look at is the coding of the system, and if that’s not the issue, take a look at the hardware. Because all of the software is coded and completed towards the end of the project, it‘s necessary to leave time for testing at this time. It is also necessary to allow time to train the office management staff who will be working with the system on a daily basis. Depending on the size of the space, this could take a few days with the lighting consultant and general contractor involved.
There’s a lot to consider when working with any new technology, especially this one that is integrated in every area of the build-out. From selecting a manufacturer, to confirming which certifications trade partners may need, the key to working with PoE lighting is plan early, pay attention to city codes, and allocate the necessary amount of time. Check out more about Clune’s nationwide capabilities here.